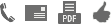
From blast pot to nozzle –
The blast machine, colloquially known as sandblasting machine, is the heart of the pressure blasting system. Attention to the proper configuration and compatibility of the machine’s components is crucial and ensures maximum blasting efficiency. Thanks to Clemco’s wealth of experience and commitment to innovation, Clemco products deliver high levels of reliability, longevity, and safety in abrasive blasting.
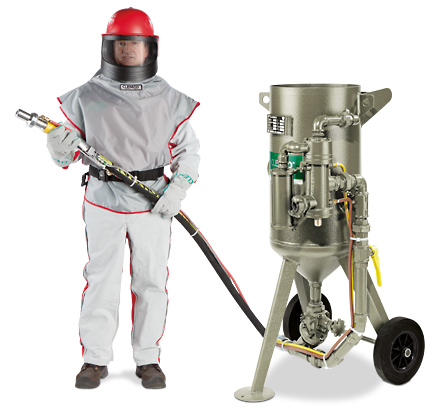
System configuration –
The proper selection of all system components in a blast machine is crucial to achieving the highest level of efficiency. Blast machine construction, capacity, media valve type, hose and nozzle, properly selected, will provide the ideal solution for any job requirement.
Our staff and distribution network can develop the optimal blast machine configuration for any application.
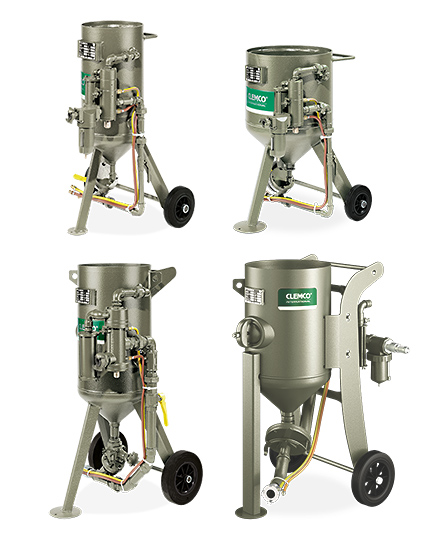
The blast pot –
Decades of experience and development form the basis for the design and construction of Clemco blast pots. Top-quality materials and state of the art production methods deliver a product with one of the longest lifetimes in the industry. Abrasive wear, an unavoidable reality, is minimized by the careful positioning of exposed components, which can be adjusted and replaced quickly. Clemco’s inventory of spare parts can keep a blast pot running for decades.
- Top-quality wear-resistant materials
- Exclusive design and high-quality finish
- CE-approved manufactured and tested
- Simple maintenance, with easy to replace spare parts
- Guaranteed parts supply
- Wide selection of standard volume sizes, from 20 I to 4500 I
- Customized solutions in the Clemco Engineering module available upon request
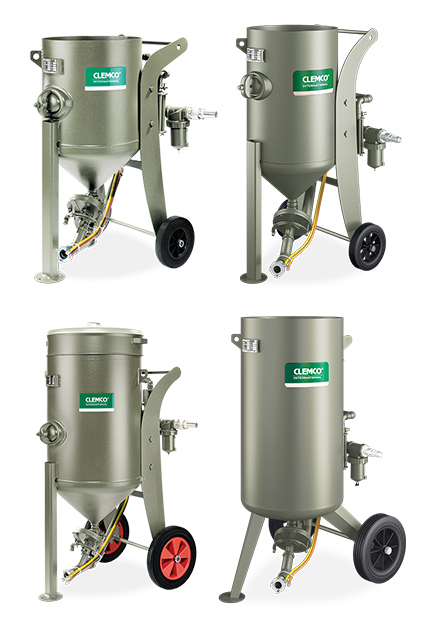
System components
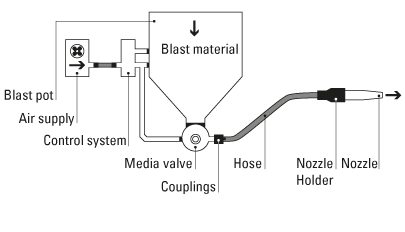
Remote control systems –
Precise operational control and safety is the hallmark of Clemco remote controls, which immediately start or stop the blast stream whenever necessary. The operator controls the blast stream independently at the nozzle, an indispensable safety feature. The blast pot can be emptied and reloaded with the engagement of the control handle, which functions on a pneumatic signal system. For longer hose lengths, Clemco recommends its low-voltage, electro-pneumatically controlled option.
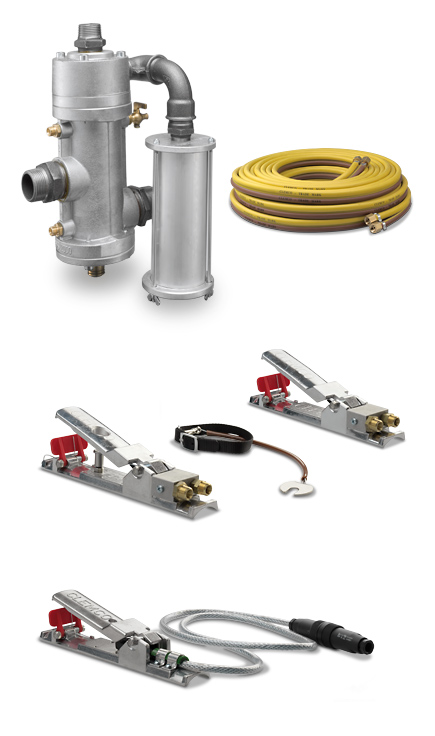
Abrasive metering valves –
Clemco-produced abrasive metering valves are constructed of high-quality, abrasive-resistant components and can suit all abrasive medias. The manual and pneumatically-controlled valves from Clemco have proven their value a thousand times over in every application.
- Optimum blast stream
- Precisely-controlled abrasive content
- Long lifetime
- Simple maintenance
- High efficiency
Clemco media valves dispense abrasive in an even, regulated flow, offsetting irregularities during pressurization and depressurization, making for consistent ease of use. Pneumatic controls respond far more quickly than manual ones, increasing operator safety through immediate start/stop control of the blast stream. The „fail-to-safe“ feature of control handle release ensures that, should the operator drop the blast hose or encounter any other problems, the blast stream stops immediately. An optional Abrasive Cutoff Switch can be added to control the media flow at the handle, allowing for an air-only blowoff stream for cleanup.
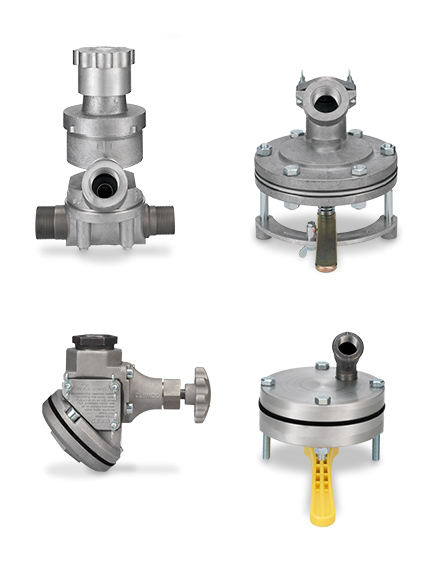
Blast hose –
Clemco offers two tiers of blast hose quality: premium and ultimate. Regardless of choice, both hose types are built with highly resistant inner lining, carbon-impregnated anti-static layers and high-durability outer wraps to guarantee a long life.
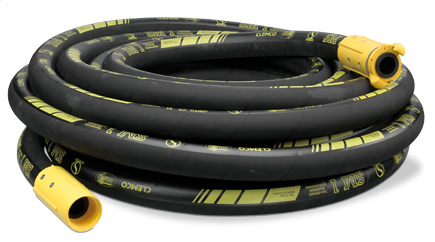
Nozzle holders and couplings –
Clemco offers an extensive range of different sizes and styles of blast nozzle holders and couplings for quick and simple replacement. Proprietary seals prevent pressure loss and turbulence at the connection, and specialized inner tooling prevents slippage from the hose, making protection and airflow assured. All seals, like the hose, are electrically conductive to prevent static shock.
The couplings and nozzle holders are made of high-quality, durable materials such as nylon, brass and aluminum, to guarantee peak levels of functionality and safety. These components are designed to function in any condition on any job site.
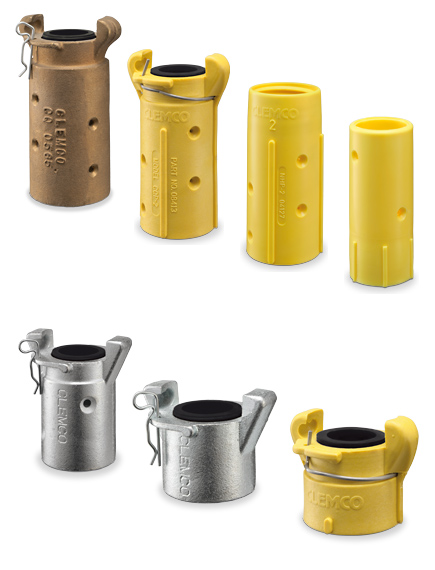
Blast Nozzles –
Clemco’s engineers consistently pursue one objective in the development of blast nozzles: greater performance with a minimum of wear. Correspondingly, Clemco blast nozzles come in a wide variety of different liners and nozzle jackets to suit any application and abrasive media. Each nozzle type has been formulated for a specific area of blast application, and the components and construction of each nozzle reflect this specificity. The available air volume, size of the workpiece, abrasive type and required surface profile all factor in critically to the proper nozzle selection.
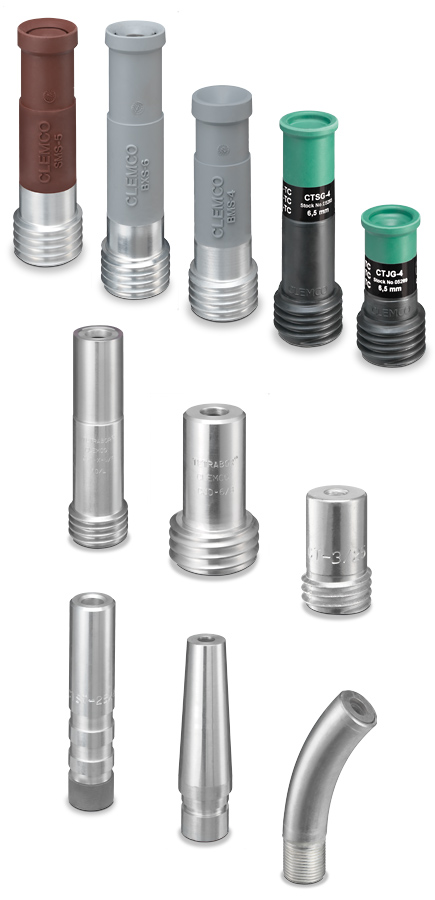