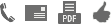
Industrial systems –
Custom-designed blast rooms are the optimal solution for large workpieces. Clemco staff methodically works with each and every customer to determine their exact blast room equipment requirements. Using this data, Clemco engineers design a blast room tailored to every specific of the job, taking into account each consideration of safety, efficiency and performance. Clemco quality blast rooms set the industry standard worldwide, and every detail reflects this commitment.
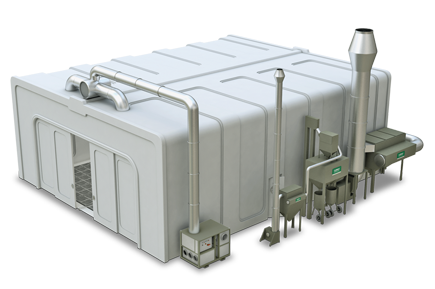
Controlled blast environments –
For decades, Clemco has been designing and planning both mobile and stationary blast facilities for nearly every blast application worldwide. Our staff analyzes a customer‘s blast work process, local safety and environmental requirements and productivity needs, and incorporates all of the above into the perfect solution for the best price. Be it upgrading and improving an existing stationary or mobile blast system or designing one from scratch, Clemco will deliver a state of the art system tailored to any need.
We size and design our blast room components to correspond directly with the parameters of workpiece size, floor space, blast application, abrasive media, process integration and safety. Customized parts handling, automated blast options, ergonomic work stations and specialized media recycling are all available and can be built to suit any specific of the blast process. Dust collectors for combined paint and blasting, metallization, dehumidification, filtration and all other air process options are also available and can be incorporated however necessary to provide the cleanest blast facility in the market.
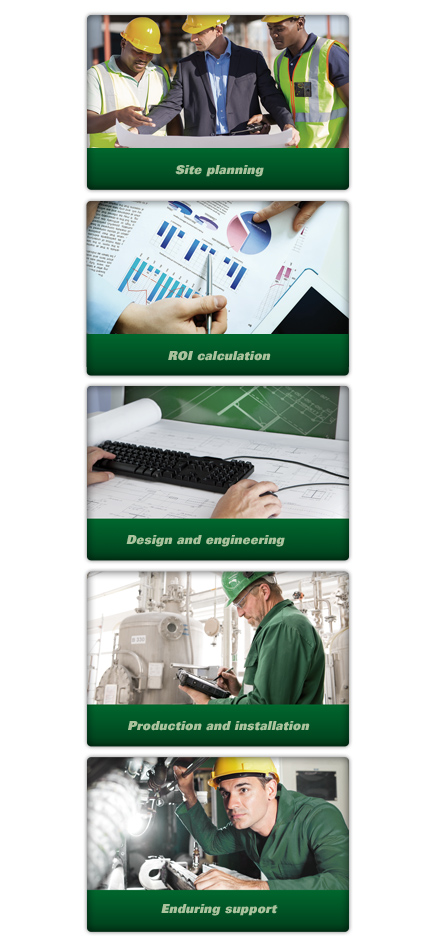
Guaranteed cost reduction –
The optimal way to blast is with the use of recyclable abrasive media, in the interest of safety, environmental protection and cost savings. Throughout its history, Clemco has designed products around the use of recyclable abrasives, with the goal in mind to keep the highest possible return of usable media to the blast pot while keeping the blast environment dust-free and safe. The mechanical and pneumatic abrasive transport systems available from Clemco provide a «closed-loop» blast process; collecting and disposing of dust, debris and worn media, while returning enormous volumes of clean abrasive quickly and reliably, providing a near-continuous blast cycle.
When designing a blast system, Clemco maintains a constant focus on a construction that is both wear-resistant and low-maintenance. Areas exposed to abrasive wear are built using extreme care, with materials selected for maximum abrasive resistance and lifetime, plus incorporating wear items that are easily replaceable. Wear points on abrasive media recovery systems are reinforced, storage silos and filtration systems sized exactly according to the abrasive, and all materials employed are of the highest possible safety rating and performance standard.
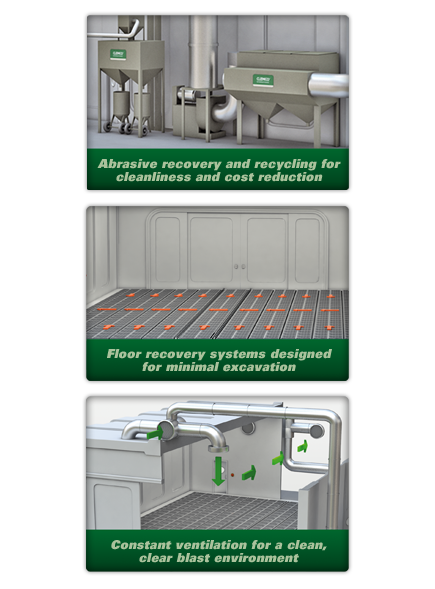
Clean air blasting –
Clemco dust collectors are among the most effective on the market. All air is ventilated from the blast room at high speed, with the filtration unit removing virtually all dust particulate from the incoming air. Clean air is essential to good visibility and surface finish in a blast room, and with a ventilated environment an operator is guaranteed to deliver a high-quality blast profile. Safety is no less a factor in Clemco’s design of its dust collectors, with all safety parameters, clean-air requirements and environmental factors accounted for in construction and installation.
Blast rooms are outfitted with strong overhead or side lighting to im-prove visibility and are also outfitted with rubber wall curtains to protect the blast enclosure from abrasive wear. Additional safety measures such as emergency exits, alarms and automated shutoff systems are included as standard by Clemco.
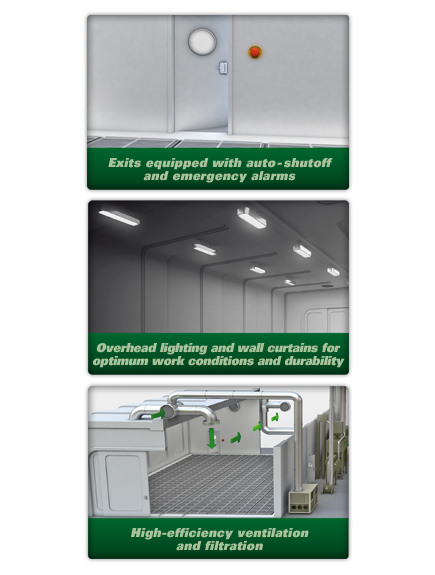
Simple components –
Clemco offers a wide range of different blast room equipment and mobile recovery components that can be used in any number of combinations to suit a vast spectrum of applications. The illustrated modules are examples of the different components that can be built into a wide selection of complex industrial systems to suit any customer’s needs.
Clemco staff will combine the best possible options for customer’s needs and ensure that performance, cleanliness and cost are constantly kept to the best possible level.
Each individual component, from the high-powered abrasive recovery system, media recycling unit, dust collector, and dehumidifier to the blast machine, performs at a peak level of technical precision and efficiency. Clemco products are enriched by decades of experience in the blast industry and are continually examined for compliance with all directives as well as performance factors and innovation potential.
Combined in optimal configurations, each industrial blast system meets each and every challenge of top-tier environmental protection, cost efficiency and industrial performance.
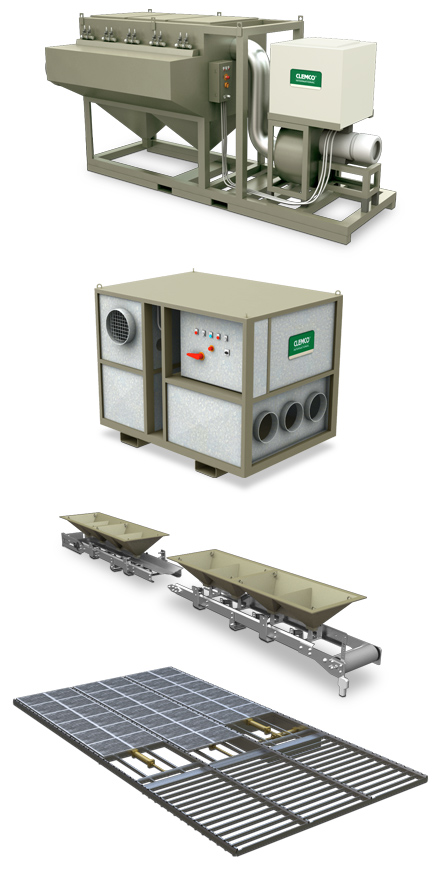
Closed cycle system components –
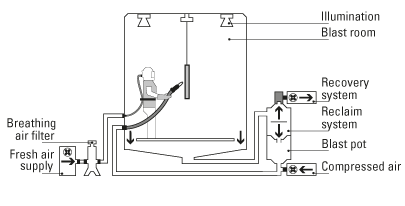